Which Techniques Effectively Translate Clinical Needs into Engineering Specifications?
Have you ever wondered how cutting-edge medical devices go from a mere concept to a life-saving tool? This article explores the crucial first step: translating clinical needs into precise engineering specifications. Beginning with a deep-dive clinical assessment and concluding with the meticulous process of needs-requirements traceability, these expert insights (six in total) will guide you through the transformative journey. Read on to uncover these valuable techniques and elevate your understanding of this complex yet fascinating process.
- Deep-Dive Clinical Assessment
- Adopt User-Centered Design
- Apply Functional Decomposition
- Engage in Risk Management Analysis
- Utilize Quality Function Deployment
- Implement Needs-Requirements Traceability
Deep-Dive Clinical Assessment
One effective technique I used to translate clinical needs into engineering specifications is to start with a deep-dive assessment of both the patient's physical needs and the specific functional goals. With over 30 years in physiotherapy and extensive experience treating musculoskeletal injuries in athletes, I've developed a keen eye for spotting underlying issues that might not be immediately obvious but are critical for sustainable recovery. This clinical insight forms the foundation for creating precise engineering requirements when designing tools, equipment, or rehab programs tailored to musculoskeletal health. For example, when we set up The Alignment Studio, we faced the challenge of designing a custom Pilates and physio suite to accommodate various levels of injury and fitness, which required balancing adaptability and stability in the equipment. Here, my clinical knowledge helped us work with engineers to specify apparatus adjustments for postural stability, joint alignment, and support customization, resulting in equipment that could be safely used by both beginners and elite athletes alike.
In practice, this involved identifying critical requirements like adjustable resistance levels, alignment guides, and ergonomic supports, and then relaying these to the design team as essential specs. I drew on my experience treating athletes and desk-bound patients alike, knowing that injury recovery needs vary significantly. This hands-on clinical insight made the engineering process more intuitive, enabling us to build equipment that meets complex therapeutic goals while enhancing patient confidence and safety. The result was a purpose-built space that empowers patients to work confidently on their recovery, ultimately translating clinical expertise into effective engineering outcomes.
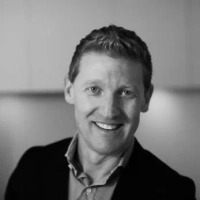
Adopt User-Centered Design
User-centered design is a method that integrates patient feedback throughout the product development process. By involving patients at every step, it ensures that their needs and preferences are thoroughly understood and addressed. This approach helps in creating solutions that are more likely to be effective and well-received by users.
It bridges the gap between clinical requirements and engineering by maintaining a focus on the end-user. Embracing this technique can lead to more patient-friendly medical technologies. Let's adopt user-centered design to make better products for patients.
Apply Functional Decomposition
Functional decomposition is a valuable approach that breaks down clinical needs into discrete engineering requirements. By simplifying complex clinical needs into smaller, manageable parts, engineering teams can focus on addressing each segment accurately. This method helps in clearly defining the specifications required to meet the overall clinical goals.
It ensures that no detail is overlooked during the product development process. When clinical needs are systematically decomposed, the final product is more likely to meet precise clinical standards. Apply functional decomposition to enhance clarity in design specifications.
Engage in Risk Management Analysis
Risk management analysis is crucial for prioritizing engineering specifications based on potential patient impact. Identifying and assessing risks early on helps in addressing and mitigating them effectively. This technique ensures that the most critical patient safety concerns are prioritized in the engineering design process.
By doing so, it enhances the overall safety and reliability of medical devices. Incorporating risk management into your design process is essential for patient safety. Engage in risk management analysis to create safer medical products.
Utilize Quality Function Deployment
Quality function deployment is a structured approach that translates customer needs into measurable design attributes. It involves detailed planning and benchmarking to ensure customer requirements are met through precise engineering specifications. This technique helps in aligning clinical needs with technical solutions by maintaining a clear focus on quality.
By converting customer feedback into actionable design attributes, product developers can ensure higher customer satisfaction. This approach ultimately leads to better performing medical devices. Utilize quality function deployment to meet and exceed customer expectations.
Implement Needs-Requirements Traceability
Formalized needs-requirements traceability is a technique that ensures alignment between clinical and engineering domains by creating a documented pathway from needs to final product specifications. This method helps in maintaining clear communication and avoids misunderstandings during the development process. It involves detailed documentation that connects initial clinical requirements directly to engineering solutions.
By adhering to this method, the entire development team remains on the same page, ensuring that the final product aligns with initial clinical goals. This practice is vital for creating reliable and effective medical devices. Implement needs-requirements traceability to maintain alignment in product development.